Stainless steel 17-4 PH (UNS J92180), Type 630, is a chromium-nickel-copper precipitation-hardening martensitic stainless steel with an addition of niobium. 17-4 PH combines high strength and hardness with good corrosion resistance. 17-4 is a common named used by two or more producers, not a trademark. And it’s not official material grade name too. In every country, it has different standard and grade.
Cast UNS J92180, ASTM A747 Grade CB7CU-1.
European standard EN10088-3: W.Nr 1.4542; X5CrNiCuNb16-4
Japan: JIS G4303; SUS630.
USA: AISI 630; ASTM A564/A693/A705-Type630; AMS5604; AMS 5622; AMS 5643; AS 7474;A564/SA693/SA705-Type630; UNS S17400
China: 0Cr17Ni4Cu4Nb; 05Cr17Ni4Cu4Nb
Casting Methods in Casting Quality Industrial:
- Sand Casting
- Investment Casting (Lost Wax Casting, Precision Casting)
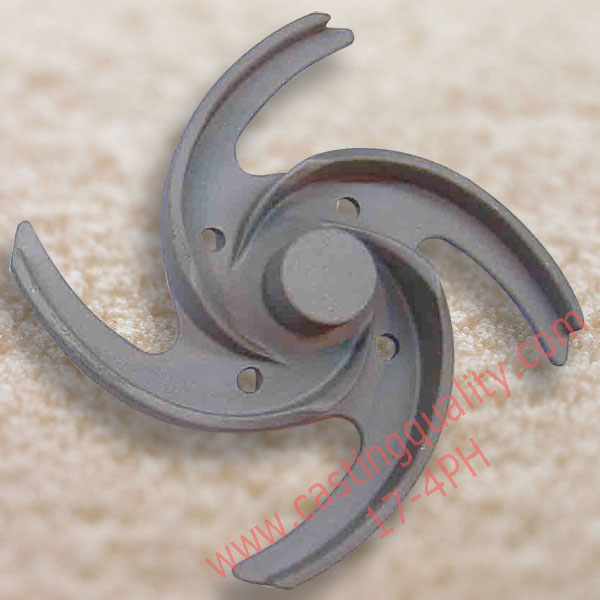
Our Services
- Sand Casting
Casting Quality focus on Metal Parts industry, we provide professional service in Metal Casting field.
Sand Casting is a popular metal form method, are suitable for all materiel, such as grey iron, ductile iron, malleable iron, carbon steel, stainless steel, aluminum and bronze.
- Investment Casting
also named as precision lost wax casting, mainly suitalbe for carbon steel and stainless steel parts. We also provide grey iron and ductile iron and aluminum and bronze parts by investment casting. It can achieve the best appearance with good tolerance
- Shell Casting
Shell casting method is a good option to replace investment casting and sand casting. the quality is better than sand casting parts, suitable for bulk production.
- CNC Machining
CNC Milling, CNC turning with 5 xix CNC center, we provide precision machining for all castings based on customers design drawings.
- CAD Design
Mechanical Design service based on customers requirement, our software is Solidworks and AutoCAD.
- Tools/Mold Design
Mould design and production will be served for metal casting ad plastic injection industry. Based on our more than 10 years experience, we supply professional molds for our customers in Europe and North American.
Reference Casting Standards and others:
ASTM A747 / A747M Standard Specification for Steel Castings, Stainless, Precipitation Hardening
ASTM A705 / A705M Standard Specifications for Age-Hardening Stainless Steel Forgings
ASTM A693 – 16 Standard Specifications for Precipitation-Hardening Stainless and Heat-Resisting Steel Plate, Sheet, and Strip
ASTM A564 / A564M Standard Specification for Hot-Rolled and Cold-Finished Age-Hardening Stainless Steel Bars and Shapes
CB7CU-1 (17-4PH) Chemical Requirements: www.castingquality.com
Standard | ASTM 747 CASTING | ASTM A705 FORING | ASTM A693 Plate/Sheet/Strip | ASTM A564 Bars/Shapes |
Grade | CB7Cu-1 (UNS J92180) | Type 630 (UNS S17400) | Type 630 (UNS S17400) | Type 630 (UNS S17400) |
Carbon | 0.07 | 0.07 | 0.07 | 0.07 |
Manganese | 0.70 | 1.00 | 1.00 | 1.00 |
Phosphorus | 0.035 | 0.040 | 0.040 | 0.040 |
Sulfur | 0.03 | 0.030 | 0.030 | 0.030 |
Silicon | 1.00 | 1.00 | 1.00 | 1.00 |
Chromium | 15.50-17.70 | 15.00-17.50 | 15.0-17.5 | 15.0-17.5 |
Nickel | 3.60-4.60 | 3.00-5.00 | 3.0-5.0 | 3.0-5.0 |
Copper | 2.50-3.20 | 3.00-5.00 | 3.0-5.0 | 3.0-5.0 |
Columbium | 0.15-0.35 | 0.15-0.45 | 0.15-0.45 | 0.15-0.45 |
Tantalum | – | |||
Nitrogen | 0.05 | – | – | – |
0Cr17Ni4Cu4Nb; 05Cr17Ni4Cu4Nb chemistry in Chinese Standard: www.castingquality.com
C:≤0.07
Si: ≤1.00
Mn:≤1.00
P:≤0.035
S:≤0.030
Ni:3.00-5.00
Cr:15.0-17.5
Mo:-
Cu:3.00-5.00
Nb:0.15-0.45
CB7CU-1 (17-4PH) Heat treatment process: All castings, whether homogenized or not, should be given a solution treatment: heating the castings and material to 1925°F (1050°C) 50F [30°C], holding the 30 min/in. [1.2 min/mm] of section but not less than 30min, and cooling to below 90°F [30°C] www.castingquality.com
Condition | PH Temperature, °F [°C] | Time, h and min | Cooling Treatment |
SA | No Precipitation hardened, solution annealing treatment. | ||
H900 | 900 [480] | 1.5 | Air cool |
H925 | 925 [495] | 1.5 | Air cool |
H1025 | 1025 [550] | 4.0 | Air cool |
H1075 | 1075 [580] | 4.0 | Air cool |
H1100 | 1100 [595] | 4.0 | Air cool |
H1150 | 1150 [620] | 4.0 | Air cool |
H1150M | 1400 [760] | 2.0 | Air cool |
1150 [620] | 4.0 | Air cool | |
H1150 DBL | 1150 [620] | 4.0 | Air cool |
1150 [620] | 4.0 | Air cool |
CB7CU-1 (17-4 PH) Mechanical Properties and Hardness
Alloy Type | PH Heat Treatment | Hardness, HB | Yield Strength 0.2% offset, min, Ksi [MPa] | Tensile Strength, min, Ksi [MPa] | Elongation in 2 in.[51mm], min, % |
CB7CU-1 (17-4PH) | H900 | 375 min | 145 [1000] | 170 [1170] | 5 |
CB7CU-1(17-4PH) | H925 | 375 min | 150 [1035] | 175 [1205] | 5 |
CB7CU-1 (17-4PH) | H1025 | 311 min | 140 [965] | 150 [1035] | 9 |
CB7CU-1 (17-4PH) | H1075 | 277 min | 115 [795] | 145 [1000] | 9 |
CB7CU-1 (17-4PH) | H1100 | 269 min | 110 [760] | 135 [930] | 9 |
CB7CU-1 (17-4PH) | H1150 | 269 min | 97 [670] | 125 [860] | 10 |
CB7CU-1 (17-4PH) | H1150M | 310 max | – | – | – |
CB7CU-1 (17-4PH) | H1150 DBL | 310 max | – | – | – |
CB7CU-1 (17-4 PH) Casting Application: www.castingquality.com
Corrosion resistance is similar to type 304, used where high strength and good corrosion resistance are required. Applications requiring high fatigue strength, good resistance to galling, seizing and stress corrosion. Suitable for intricate parts requiring machining and welding.
- Aerospace — structural and parts
- Propeller shafts pump shafts, pins, and valve spindles
- Biomedical — hand tools
- Chemical Processing
- Food Process Equipment
- Gate Valves
- Mechanical Components
- Nuclear Waste Processing and Storage
- Oil and Gas Production — foils, helicopter deck platforms, etc.
- Pulp and Paper — paper mill equipment
Heat Treatments for 17-4PH and Their Designation www.castingquality.com
Designation | Processing |
Condition A* SA | Heated at 1900°F ± 25°F for 1/2 hour, air (Solution treated) cooled or oil quenched to below 90°F. Normally performed at mill. |
H 1075, H 1150 | Condition A material heated at 1075 or 1150°F ± 15°F for 4 hours and air cooled. |
H 900
| Condition A material heated at 900°F ± 15°F for 1 hour and air cooled. Maximum hardness but low toughness. Sensitive to stress corrosion cracking. |
H 925, H 1025, H 1100 | Condition A material heated at specified temperature for 4 hours and air cooled. |
H 1150-M | Condition A material heated at 1400 ± 25°F for 2 hours, air cooled, then heated at 1150 ± 15°F for 4 hours and air cooled. This heat treatment used for maximum toughness, and for cryogenic applications to -320°F. |
17-4PH WELDABILITY:
17-4PH has been welded by GTAW, GMAW, SMAW, PAW, Electron-beam (EB) and resistance welding. For GMAW a shielding gas of 75% argon and 25% helium is suggested.
Sections up to 1” thick are normally welded in the annealed (A) condition. Highly restrained joints or heavier sections are best welded in conditions H1100 or H1150. Welding of 17-4PH in conditions H900 through H1075 is not recommended.
No preheat is usually necessary for sections up to 4” thick. For restrained welds a 200-300°F (100-150°C) pre-heat is beneficial.
Matching composition ER630 wire or E630 covered electrodes (AMS 5803, 5825 or 5827) are normally used. Joints to carbon or low alloy steel may be made with ERNiCr-3 wire (alloy 82) or ENiCrFe-3 covered electrodes (alloy 182).
Post-weld heat treatment (PWHT) is required. For single pass welds on condition A base metal, simply aging to condition H 900 through H 1150 usually suffices (H 900 condition has very low notch toughness). For multipass welds the structure should be solution annealed after welding, followed by an aging treatment 900-1150ºF.
Notches must be avoided, and partial penetration welds with their built-in notches are quite undesirable. If design considerations force the use of partial penetration welds consider making the root pass only with ERNiCr-3 (alloy 82) wire to minimize notch sensitivity.
17-4PH Machining:
Typical machining speeds for 17-4PH, using high speed steel tools are:
Operation Speed Feed
SFPM IPR
Turning, 80-95 0.015-0.007
Single Point
Drilling 1/4” dia 50 0.004
3/4” dia 50 0.008
Reaming
under 1/2” 60 0.003
over 1/2” 60 0.008
Die Threading
3–7 1/2 TPI 5-12 —
8–15 TPI 8-15 —
over 16 TPI 10-20 —
Tapping 12-25 —
Milling, End 85 0.001-0.004
and Peripheral
Broaching 10
When using carbide tools, surface speed feet/minute (SFPM) may be increased 2 to 3 times over high speed suggestions. Feeds can be increased 50 to 100%.
17-4 PH Hot Forming
Heat uniformly at 1742 – 2192°F (950 –1200°C). A full solution anneal, cooling lower than 76°F (25°C) and aging at the required temperature must occur after hot forming. The post forming heat treatment should be a function of the desired mechanical properties.
17-4 PH Cold Forming
Alloy 17-4PH has limited cold forming properties. Cold forming can only be undertaken on plates in the fully annealed condition. Stress corrosion resistance is enhanced by re-aging at the precipitation hardening temperature after cold working.
17-4 PH Cutting
Thermal cutting operations such as plasma cutting should be avoided. Mechanical cutting operations such as band saw, abrasive water jet, shearing and machining are preferred.
Nice article. Informative. One question, why is the solution annealing temperature for castings lower than the solution annealing temperature for plate?
Because plates are/can be added on later or at any other time. They can also be stripped off and rebuilt in the rebuilding process if a company has there products rebuilt.