Introduction of ASTM A436 Austenitic Gray Iron
Austenitic Gray Iron castings in ASMT A48 are used primarily for resistance to heat, corrosion and wear. It’s characterized by uniformly distributed graphite flakes, some carbides and the presence of sufficient alloy content to produce an austenitic structure. It’s a Ni-Resist cast iron.
Manufacture Process for ASTM A436 Austenitic Gray Iron
- Sand Casting
- Shell Casting
- Lost Foam Casting
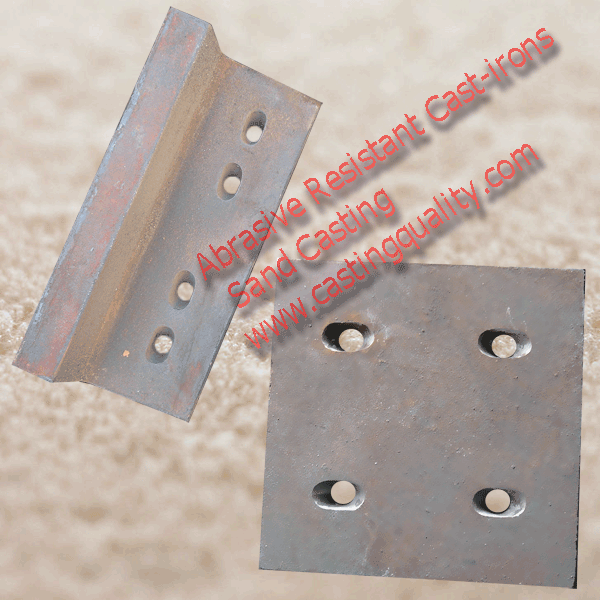
Our Services
- Sand Casting
Casting Quality focus on Metal Parts industry, we provide professional service in Metal Casting field.
Sand Casting is a popular metal form method, are suitable for all materiel, such as grey iron, ductile iron, malleable iron, carbon steel, stainless steel, aluminum and bronze.
- Investment Casting
Also named as precision lost wax casting, mainly suitalbe for carbon steel and stainless steel parts. We also provide grey iron and ductile iron and aluminum and bronze parts by investment casting. It can achieve the best appearance with good tolerance
- Shell Casting
Shell casting method is a good option to replace investment casting and sand casting. the quality is better than sand casting parts, suitable for bulk production.
- Permanent Mold Casting
For aluminum parts and Brozne parts
- CNC Machining
CNC Milling, CNC turning with 5 xix CNC center, we provide precision machining for all castings based on customers design drawings.
- CAD Design
Mechanical Design service based on customers requirement, our software is Solidworks and AutoCAD.
- Tools/Mold Design
Mould design and production will be served for metal casting ad plastic injection industry. Based on our more than 10 years experience, we supply professional molds for our customers in Europe and North American.
Standard of ASTM A436 Austenitic Gray Iron
ASTM A436-84 Standard Specification for Austenitic Gray Iron Castings
ASTM A436 Austenitic Gray Iron Equivalent Material Grades
n/a
ASTM A436 Austenitic Gray Iron Material Property
Density: 7.8 kgs/dm3
ASTM A436 Austenitic Gray Iron Casting Chemical Composition Requirements
Grade | Chemical Composition / Physical Properties % (max, except where range is given) | |||||||||
Standard | Grade | Carbon | Silicon | Manganese | Nickel | Copper | Chromium | Sulfur | Molybdenum | |
ASTM A436 Type 1 | 3.00 | 1.0-2.8 | 0.5-1.5 | 13.5-17.5 | 5.5-7.5 | 1.5-2.5 | 0.12 | – | ||
ASTM A436 Type 1b | 3.00 | 1.0-2.8 | 0.5-1.5 | 13.5-17.5 | 5.5-7.5 | 2.5-3.5 | 0.12 | – | ||
ASTM A436 Type 2 | 3.00 | 1.0-2.8 | 0.5-1.5 | 18.0-22.0 | 0.5 | 1.5-2.5 | 0.12 | – | ||
ASTM A436 Type 2b | 3.00 | 1.0-2.8 | 0.5-1.5 | 18.0-22.0 | 0.5 | 3.0-6.0 | 0.12 | – | ||
ASTM A436 Type 3 | 2.60 | 1.0-2.0 | 0.5-1.5 | 28.0-32.0 | 0.5 | 2.5-3.5 | 0.12 | – | ||
ASTM A436 Type 4 | 2.60 | 5.0-6.0 | 0.5-1.5 | 29.0-32.0 | 0.5 | 4.5-5.5 | 0.12 | |||
ASTM A436 Type 5 | 2.4 | 1.0-2.0 | 0.5-1.5 | 34.0-36.0 | 0.5 | 0.1 | 0.12 | |||
ASTM A436 Type 6 | 3.0 | 1.5-2.5 | 0.5-1.5 | 18.0-22.0 | 3.5-5.5 | 1.0-2.0 | 0.12 | 1.0 |
ASTM A436 Austenitic Gray Iron Casting Mechanical Property
Grade | Mechanical Requirements | |||
Standard | Grade | Tensile Strength, min, ksi | Tensile Strength, min, (MPa) | Brinell Hardness (3000kg) |
ASTM A436 Type 1 | 25 | 172 | 131-183 | |
ASTM A436 Type 1b | 30 | 207 | 149-212 | |
ASTM A436 Type 2 | 25 | 172 | 118-174 | |
ASTM A436 Type 2b | 30 | 207 | 171-248 | |
ASTM A436 Type 3 | 25 | 172 | 118-159 | |
ASTM A436 Type 4 | 25 | 172 | 149-212 | |
ASTM A436 Type 5 | 20 | 138 | 99-124 | |
ASTM A436 Type 6 | 25 | 172 | 124-174 |
Austenitic Gray Iron Magnetic Property in ASMT A436
A convenient shop test for differentiating the various types of austenitic gray iron is based on the fact that a ground
face of either the test bars or the castings of Types 1, 2, and 4 will not attract a small steel horseshoe-type magnet, that is normally attracted to steel. Types 1b, 2b, 3, and 5 may be attracted to a magnet. This nonmagnetic test is a convenient qualitative test only for Types 1, 2, and 4 and shall not be used as a basis for acceptance. In the event that nonmagnetic castings are specified, the magnetic permeability test shall be used. The specific test conditions and magnetic permeability limits shall be agreed upon between the manufacturer and the purchaser.
ASTM A436 Austenitic Gray Iron Heat Treatment Requirement
Bye agreement between the manufacturer and the purchaser, the castings may be stress relieved by heating to and holding in the temperature range from 1150 to 1200°F (620 to 650°C) for not less than 1 nor more than 2 h/in. of thickness in the thickest section. Heating and cooling shall be uniform and shall be not more than 400°F (222°C)/h for castings less than 1 in. in maximum thickness, nor more than 400°F/h divided by the maximum section thickness in inches for thicker castings. During the cooling cycle, castings may be cooled in still air after temperature has dropped to 600°F (315°C).
If the manufacturer can demonstrate that another treatment provides satisfactory stress relief, it may be used by agreement between the manufacturer and the purchaser.
Whenever dimensional changes in high-temperature service are a problem, by agreement between the manufacturer and the purchaser, the castings may be stabilized by heating at 1600°F (870°C) for 1 h/in. of section, for a minimum of 1 h. Otherwise, the austenite that is supersaturated with respect to carbon may reject carbon during service and produce dimensional changes.
By agreement between the manufacturer and the purchaser, castings with chilled edges or excessive carbides may be annealed at 1750 to 1900°F (955 to 1040°C) for 1⁄2 to 5 h, followed by uniform cooling, preferably in still air.
ASTM A436 Austenitic Gray Iron Castings Application
- Pump and valve
- piston ring inserts
- bearings
- cylinder liners
Tips
Austenitic Gray Iron castings shall not be repaired by welding, plugging, or other methods without written permission from the purchaser.
As a professional manufacturer in China, We Casting Quality focus on Metal Parts OEM industry, and provide solutions and services in Metal Casting field as following:
- Sand Casting
- Investment Casting, Lost Wax process
- Shell Casting
- Lost Form Casting
- CNC Machining
- CAD Design
- Tools/Mold Design
Material Supplied
- Cast Iron Castings (Grey Iron, Malleable Iron, Ductile Iron)
- Carbon Steel and Alloy Steel Castings
- Stainless Steel and Duplex Stainless Steel Castings
- Aluminum Castings
- Bronze and Brass Castings
- Titanium and Cobalt Alloy Castings
What We Can Do
- Design Ability
Our engineers will help you to improve the designs based on casting technology, then The simulation software will be processed to verify the casting pouring system. Pro/E, Solidworks, AutoCAD and ProCast are available in Casting Quality Industrial.
- Saving Cost
Some manufacture processes may lead high cost. We will analyse the designs and advise the suitable methods to our customers. The best solution will be adopted.
- Quality Control
From the raw material selecting to bulk production processing, all procedures will follow PPAP program if necessary. The certificates will be provided including chemistry, hardness, mechanical property or NDT testing.
- Production Capacity
The max iron/steel castings can reach 30tons in weight, meanwhile the minus casting is around 1gram only.
We also have prototyping and 3D scanning ability for sample plan.
- Logistic Service
The products will be delivered directly to customer’s workshop, which will save plenty of work for clients.