In a low-alloy steel casting, the alloying elements are present in percentages greater than the following: Mn, 1.00; Si, 0.70; Cu, 0.50; Cr, 0.25; Mo, 0.10; V, 0.05; W, 0.05; and Ti, 0.05. Limitations on phosphorus and sulfur contents apply to low-alloy steels as well as carbon steels unless they are specified to be different for the purpose of producing some desired effect, e.g., free machining. Carbon and low-alloy steels account for approximately 85 percent of the steel castings produced in the United States.
4130/4140 alloy steel is suitable for investment casting( precision lost wax casting) method. also can be make by sand casting, but the grade is named different.
IC4130 is same as AISI 4030 , and IC4140 same as AISI 4140. They are steel grade for investment casting.
AISI 4130: IC 4130, AMS 5336 D, ASTM A-148, ASTM A-732 GR 7Q, MIL-S-22141, C11011102, C11577275
AISI 4140: IC 4140, AMS 5338 C, ASTM A-148, ASTM A-732 GR 8Q, MIL-S-22141, C11011102, C11577275
Those two grade are popular used in the quenched and tempered condition for strength. Applications include machinery parts where strength and hardness are requisites.
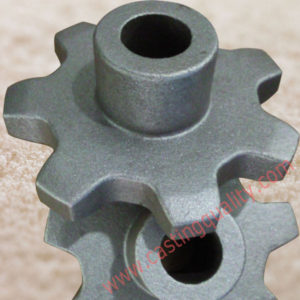
Casted Sprocket-precision investment casting
In Casting purpose, it’s origin from ASTM A732 Standard Specification for Castings, Investment, Carbon and Low Alloy Steel for General Application, and Cobalt Alloy for High Strength at Elevated Temperatures:
7Q, IC 4130:
C: 0.25-0.35; Mn 0.4-0.70; P 004; S 0.045; Si 0.20-0.80; Cr 0.80-1.10; Mo 0.15-0.25; (Cu 0.50, W 0.10)
Mechanical Properties: Tensile 150Ksi(1030Mpa), Yield 115Ksi(793MPa), Elongation 7%, Heat treatment Quench Temper
8Q, IC 4140
C: 0.35-0.45; Mn 0.70-1.00; P 004; S 0.045; Si 0.20-0.80; Cr 0.80-1.10; Mo 0.15-0.25; (Cu 0.50, Ni 0.50, W 0.10)
Mechanical Properties: Tensile 180Ksi(1241Mpa), Yield 145Ksi(1000MPa), Elongation 5%, Heat treatment Quench Temper
In ASTM A29, Standard Specification for Steel Bars, Carbon and Alloy, Hot-Wrought, General Requirements
4130: C:0.28-0.33; Mn 0.4-0.60; P 0.035; S 0.040, Si 0.15-0.35; Cr 0.80-1.10; Mo 0.15-0.25
4140: C:0.38-0.43; Mn 0.75-1.00; P 0.035; S 0.040, Si 0.15-0.35; Cr 0.80-1.10; Mo 0.15-0.25
4130 can be heated at 1600 F followed by an oil quench, The best results a normalizing pre-hardening heat treatment may be used at 1650 to 1700 F followed by the 1600 F soak and oil quench.
4140: This alloy is hardened by heating to 1550 F and quenching in oil. It is best to normalize the alloy by heating at 1675 F for a long enough time to permit thorough heating, followed by air cooling, prior to the hardening treatment.
The temper process will be defined by different usage.
American Specification, what mean the steel grade number:
This designation has been standardized by SAE and AISI. A 2- and 3- degit number signifies the composition range of alloying elements followed by a 2 digit number referring to average carbon content in hundredths of a percent. Some of the most generally used steels are as bellow:
10XX — Plain carbon steel
13XX — Manganese 1.75 steel
25XX – Nickel 5.0 steel
31XX – Nickel 1.25; Chromium 0.65
40XX – Molybdenum 0.25 steel
41XX – Chromium 0.50 or 0.95; Molybdenum 0.12 or 0.20
43XX – Nickel 1.80; Chromium 0.50 or 0.80; Molybdenum 0.25
44XX – Manganese 0.80; Molybdenum 0.40
46XX – Nickel 1.85; Molybdenum 0.25
51XX – Chromium 0.80, 0.88, 0.93, 0.95 or 1.00
61XX – Chromium 0.60, 0.80 or 0.95; Vanadium 0.12 or 0.10 min or 0.15 min
81XX – Nickel 0.30; Chromium 0.40; Molybdenum 0.12
92XX – Manganese 0.85; Silicon 2.00
93XX – Nickel 3.25; Chromium 1.20; Molybdenum 0.12