Introduction of ASTM A532 Class I type D Designation Ni-HICr
Ni-HICr is a popular abrasion resistant cast iron in ASTM A532 standard Class I type D; This material has high chrome content of 7-11%, and it is one type of White Iron.
Manufacture Process for ASTM A532 Class I type D Designation Ni-HICr
- Sand Casting
- Shell Casting
- Lost Foam Casting
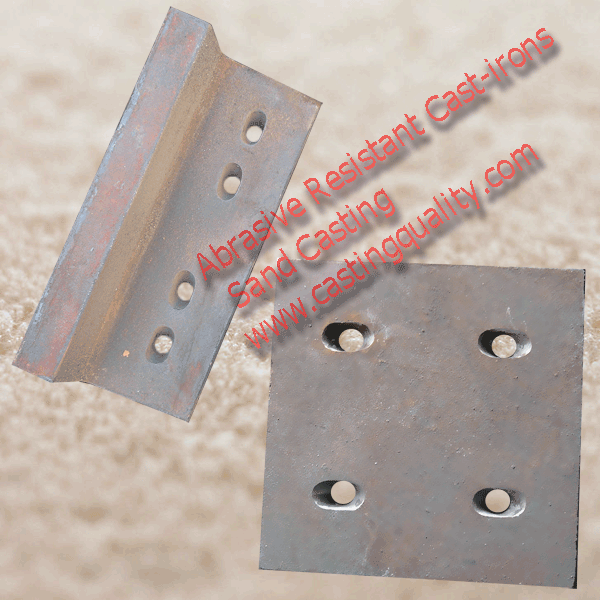
Our Services
- Sand Casting
Casting Quality focus on Metal Parts industry, we provide professional service in Metal Casting field.
Sand Casting is a popular metal form method, are suitable for all materiel, such as grey iron, ductile iron, malleable iron, carbon steel, stainless steel, aluminum and bronze.
- Investment Casting
Also named as precision lost wax casting, mainly suitalbe for carbon steel and stainless steel parts. We also provide grey iron and ductile iron and aluminum and bronze parts by investment casting. It can achieve the best appearance with good tolerance
- Shell Casting
Shell casting method is a good option to replace investment casting and sand casting. the quality is better than sand casting parts, suitable for bulk production.
- Permanent Mold Casting
For aluminum parts and Brozne parts
- CNC Machining
CNC Milling, CNC turning with 5 xix CNC center, we provide precision machining for all castings based on customers design drawings.
- CAD Design
Mechanical Design service based on customers requirement, our software is Solidworks and AutoCAD.
- Tools/Mold Design
Mould design and production will be served for metal casting ad plastic injection industry. Based on our more than 10 years experience, we supply professional molds for our customers in Europe and North American.
Content for ASTM A532 Class I type D Designation Ni-HICr
Standard of ASTM A532 Class I type D Designation Ni-HICr
ASTM A532 Standard Specification for Abrasion-Resistant Cast Irons
ASTM A532 Class I type D Designation Ni-HICr Equivalent Material Grades
EN 12513 Grade EN-GJN-HB550 EN 5.5605
DIN 1695 Grade G-X 300 CrNiSi 9 5 2 (DIN 0.9630)
ASTM A532 Class I type D Designation Ni-HICr Material Property
Density: 7.8 kgs/dm3
ASTM A532 Class I type D Designation Ni-HICr Casting Chemical Composition Requirements
Standard | ASTM A532 |
Class | I |
Type | D |
Designation | Ni-HICr |
Carbon % | 2.5-3.6 |
Manganese % | 2.0 max |
Silicon % | 2.0 max |
Nickel % | 4.5-7.0 |
Chromium % | 7.0-11.0 |
Molybdenum % | 1.5 max |
Copper % | – |
Phosphorus % | 0.10 max |
Sulfur % | 0.15 max |
ASTM A532 Class I type D Designation Ni-HICr Casting Mechanical Property
No requirement about tensile/yield or elongation.
ASTM A532 Class I type D Designation Ni-HICr Casting Hardness
Standard | ASTM A532 | |
Class | I | |
Type | D | |
Designation | Ni-HICr | |
As Cast or As cast and Stress relieved | 500HB/50GBR/540HV | |
Hardened or Hardened and Stress Relieved | Level 1 | 600HB/56HRC/660HV |
Level 2 | 650HB/59HRC/715HV w | |
Chill Cast, min | 550HB/53HRC/600HV | |
Softened, max | – |
ASTM A532 Class I type D Designation Ni-HICr Heat Treatment Requirement
It will be up to the hardness requirement: as Cast, as Cast and Stress relieved, Hardened, Hardened and stress relieved, Softened for machining.
ASTM A532 Class I type D Designation Ni-HICr Castings Application
- Pump industry.
- Mining industry, crusher liner, chute liner.
- Oil or recycling.
What is White Iron?
When white iron solidifies, virtually all the carbon appears in the form of carbides, White irons are hard and brittle, and they break with a white fracture. These irons are usually alloyed with Chromium and Nickel. The hardness is in the range of 500 to 600 BHN, the specific alloying that is required in a function of section size and application; there must be coordination between designer and foundry. These irons exhibit outstanding wear resistance and are used extensively in the mining industry for ball mill shell liners, balls, impellers, and slurry pumps.
As a professional manufacturer in China, We Casting Quality focus on Metal Parts OEM industry, and provide solutions and services in Metal Casting field as following:
- Sand Casting
- Investment Casting, Lost Wax process
- Shell Casting
- Lost Form Casting
- CNC Machining
- CAD Design
- Tools/Mold Design
Material Supplied
- Cast Iron Castings (Grey Iron, Malleable Iron, Ductile Iron)
- Carbon Steel and Alloy Steel Castings
- Stainless Steel and Duplex Stainless Steel Castings
- Aluminum Castings
- Bronze and Brass Castings
- Titanium and Cobalt Alloy Castings
What We Can Do
- Design Ability
Our engineers will help you to improve the designs based on casting technology, then The simulation software will be processed to verify the casting pouring system. Pro/E, Solidworks, AutoCAD and ProCast are available in Casting Quality Industrial.
- Saving Cost
Some manufacture processes may lead high cost. We will analyse the designs and advise the suitable methods to our customers. The best solution will be adopted.
- Quality Control
From the raw material selecting to bulk production processing, all procedures will follow PPAP program if necessary. The certificates will be provided including chemistry, hardness, mechanical property or NDT testing.
- Production Capacity
The max iron/steel castings can reach 30tons in weight, meanwhile the minus casting is around 1gram only.
We also have prototyping and 3D scanning ability for sample plan.
- Logistic Service
The products will be delivered directly to customer’s workshop, which will save plenty of work for clients.